After their adventures of 2021, it's time to revisit and rework the design of the Penelopean Woven Robots. These robots were originally created to weave braids around a maypole, which after a few attempts, they eventually did successfully. Their form and construction depicts a kind of alternative future where the ancient Greeks went on to design modern technology embedded with their science of the woven cosmos.
Originally intended as a physical performance in the usual sense, during the trials of 2020 and 2021 they became a way for people to dance together in the same physical space, remotely. Now as part of the Alpaca project it's time to build some more. We don't necessarily wish to add features or expand their abilities, but we want to explore different ways of programming them, look more at combining their movements with sounds and musical patterns, and we'd also like to have enough to be able to send them to venues to carry out their own remote performances without us.
The focus is moving from prototype to mass production, we have spent some time simplifying the circuit board, reducing the parts count and making them faster to build. The global situation with components is different now - using socketed microprocessors has aged well, reuse of these now all too valuable parts between projects and over time become much more important.
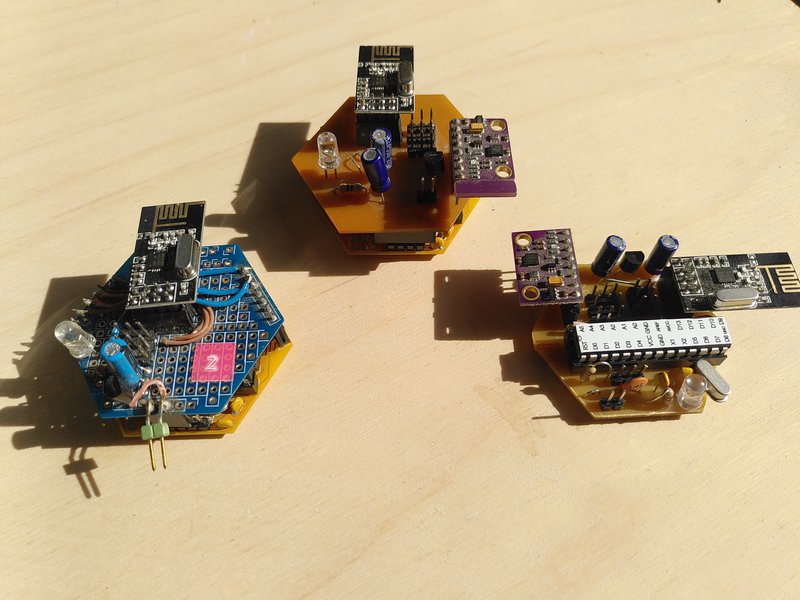
Here you can see the three major iterations of the robot control circuit, the first prototype on the left, current version in the middle and the first version of this new design on the right. We've consolidated the circuit into one board, by removing the need for two layers sandwiched together, this was mainly done so the microcontroller board was itself reusable, but we can remove the need for a lot of connectors and space if we bring them together and put the radio and sensors on the same one. We also save space and fabrication time if we remove the connector for the programmer, and program them before inserting them into the socket - now that the firmware is relatively stable this is more feasible.
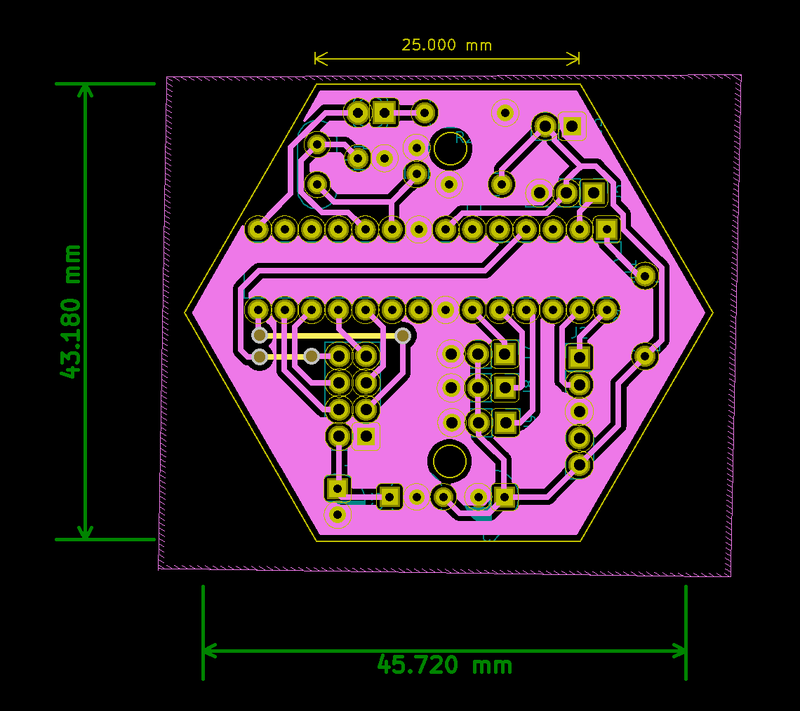
This is the design for the new circuit, which took a surprisingly long time to get right, but can now be quickly CNC machined. CNC remains our fabrication method of choice even at scale, for a variety of reasons. One is that it removes the need for a lot of secondary materials and infrastructure, and the other is that in a project like this, it provides an end result that elicits a different response in people to a more standard approach. It has a visibly "home manufactured" look which brings it closer to the woven technology. Finding ways to highlight the equivalence of "digital" and "physical" concepts and artefacts (or in this case reduce the separation between them) is really a central motivation for this work.
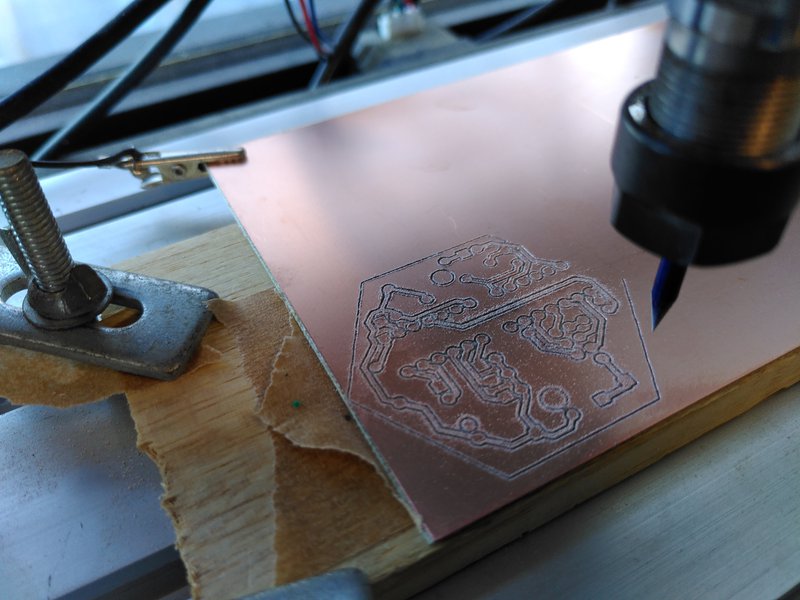
Moving on to weaving the robots structure, this largely remains the same as we have a good way to arrange the servos to provide the best movements which we don't want to mess with. However there are a few tweaks, one is to maximise the length of warp on the loom better, so we can squeeze out more robots at a time:
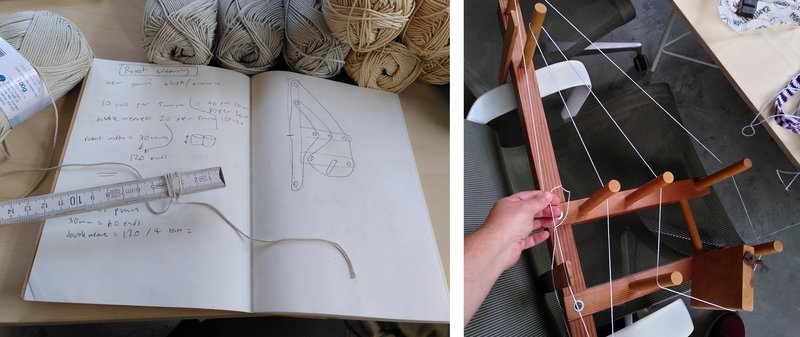
The other is to weave in serial numbers of the robots as a binary code pattern. In the previous robots we had to put little coloured paper collars around them so people could tell which one they were controlling. I doubt this approach will be visible enough for use remotely (there are some other ideas for that, more on them soon), but it should be much better in a physical performance, and again highlights the digital nature of weaving.
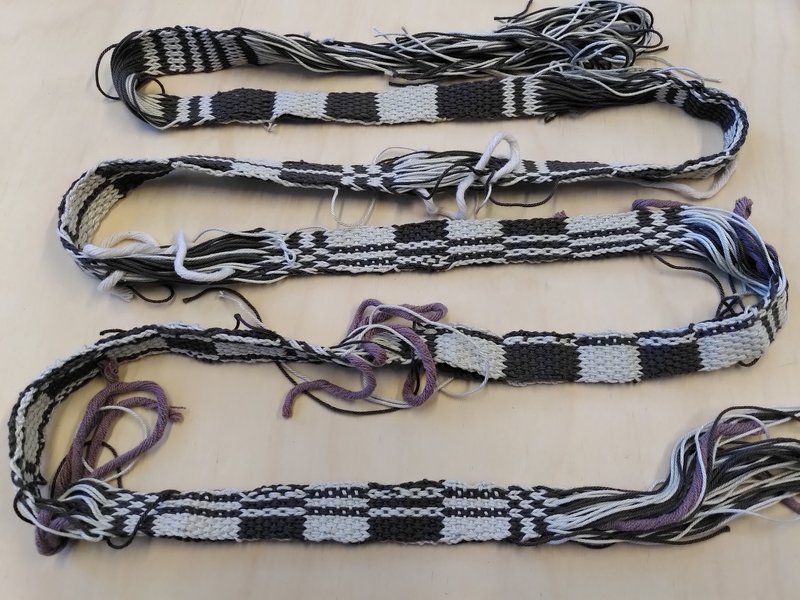
With such a long warp, there were problems with tension - which gradually increased during weaving, and while there is a built in tension control, it eventually maxed that out and was in danger of breaking the inkle loom. A quick hack was required to release some tension to get the last two robots finished. As with code problems being all too often solved by more code, textile problems are usually solved by more textiles.
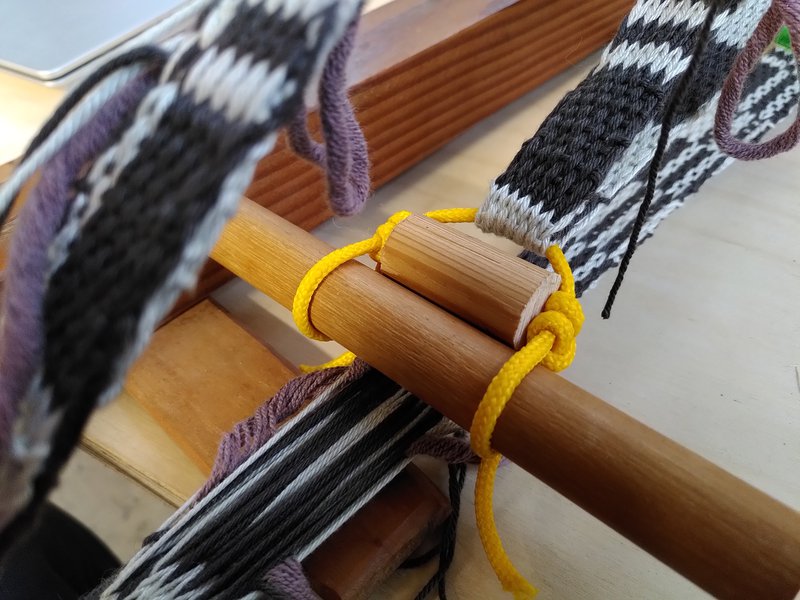
We plan to make at least another sixteen robots, giving us two sets in total, and a few spares would be good too. We are now gradually machining the circuit boards we need, and will start final assembly and testing of this first batch soon. After that we can set up the loom again and start the a second batch.